BLDC motor control algorithm
Brushless motors are self-conversion type (self-direction conversion), so the control is more complicated.
BLDC motor control requires knowledge of the rotor position and mechanism of the motor for rectifying steering. For closed loop speed control, there are two additional requirements for measuring rotor speed / or motor current and PWM signal to control motor speed power.
The BLDC motor can be arranged with side or center-aligned PWM signals depending on the application requirements. Most applications require only speed change operations and will use six independent edges to align the PWM signals. This provides the highest resolution. If the application requires server positioning, energy braking or power reversal, it is recommended to use a complementary center-aligned PWM signal. To sense the rotor position, the BLDC motor uses a Hall effect sensor to provide absolute position sensing. This leads to more line usage and higher costs. The sensorless BLDC control eliminates the need for a Hall sensor and uses the back EMF (electromotive force) of the motor to predict the rotor position. Sensorless control is critical for low-cost variable speed applications like fans and pumps. Refrigerator and air conditioner compressors also require sensorless control when using BLDC motors.
Insertion and replenishment of dead time
Most BLDC motors do not require complementary PWM, dead time insertion or dead time compensation. BLDC applications that may require these features are only high performance BLDC servo motors, sinusoidally excited BLDC motors, brushless AC, or PC synchronous motors.
Control algorithm
Many different control algorithms are used to provide control of the BLDC motor. Typically, a power transistor is used as a linear regulator to control the motor voltage. This method is not practical when driving high power motors. High power motors must be PWM controlled and require a microcontroller to provide start and control functions.
The control algorithm must provide the following three functions:
· PWM voltage for controlling motor speed · Mechanism for reversing the motor reversing · Method for predicting rotor position using back EMF or Hall sensor
Pulse width modulation is only used to apply variable voltages to the motor windings. The effective voltage is proportional to the PWM duty cycle. When properly commutated, the torque speed characteristics of the BLDC are the same as for a DC motor. A variable voltage can be used to control the speed and variable torque of the motor. The commutation of the power transistors enables the proper windings in the stator to produce the optimum torque based on the rotor position. In a BLDC motor, the MCU must know the position of the rotor and be able to commutate at the right time.
Trapezoidal commutation of BLDC motor
One of the easiest ways to brush a DC brushless motor is to use a so-called trapezoidal commutation.
In this schematic, the current is controlled by a pair of motor terminals each time, and the third motor terminal is always electronically disconnected from the power supply.
The three Hall devices embedded in the large motor are used to provide digital signals that measure the rotor position in a 60 degree sector and provide this information on the motor controller. Since the amount of current on each of the two windings is equal and the current on the third winding is zero, this method can only produce a current space vector having one of six directions. With the steering of the motor, the current at the motor terminal is once switched (rectified commutation) at 60 degrees per revolution, so the current space vector is always at the position closest to 30 degrees of the phase shift of 90 degrees.
Therefore, the current waveform of each winding is trapezoidal, starting from zero to positive current and then to zero and then to negative current.
This produces a current space vector that will approach the equilibrium rotation as it steps up in six different directions as the rotor rotates.
In motor applications like air conditioning and frost, the use of Hall sensors is not a constant choice. A back EMF sensor induced in a non-coupling winding can be used to achieve the same result. Such trapezoidal drive systems are very common due to the simplicity of their control circuits, but they suffer from torque ripple problems during the rectification process.
Sinusoidal rectification commutation of BDLC motors
Trapezoidal commutation is not enough to provide balanced, accurate brushless DC motor control. This is mainly because the torque generated in a three-phase brushless motor (with a positive wave back electromotive force) is defined by the following equation:
Shaft torque = Kt [IR Sin(?) + IS Sin(?+120) + IT Sin(?+240)]
among them
? The electrical angle of the shaft
Kt is the torque constant of the motor
IR, IS, and IT are phase currents.
If the phase current is sinusoidal: IR = I0Sin?; IS = I0Sin (+120?); IT = I0Sin (+240?) will get
Shaft torque = 1.5I0*Kt (a constant independent of the angle of the shaft)
The sinusoidal commutating brushless motor controller strives to drive three motor windings with three currents that smoothly sinusoidal as the motor rotates. The relevant phases of these currents are chosen such that they will produce a smooth rotor current space vector with directions that are orthogonal to the rotor and have invariants. This eliminates the torque ripple and steering pulses associated with the northward steering.
OREMA UN series 12V AGM batteries represent the zenith of sealed lead acid battery technology. Fabricated with ultra-high purity lead, these 12V Rechargeable batteries set the standard in performance and durability, serving a multitude of applications with unmatched efficiency.OREMA 12V AGM Battery is designed for diverse applications, from emergency backup and renewable energy systems to UPS and recreational vehicles. Their robust construction and reliable performance make them suitable for a wide array of uses, ensuring uninterrupted operation in critical situations.
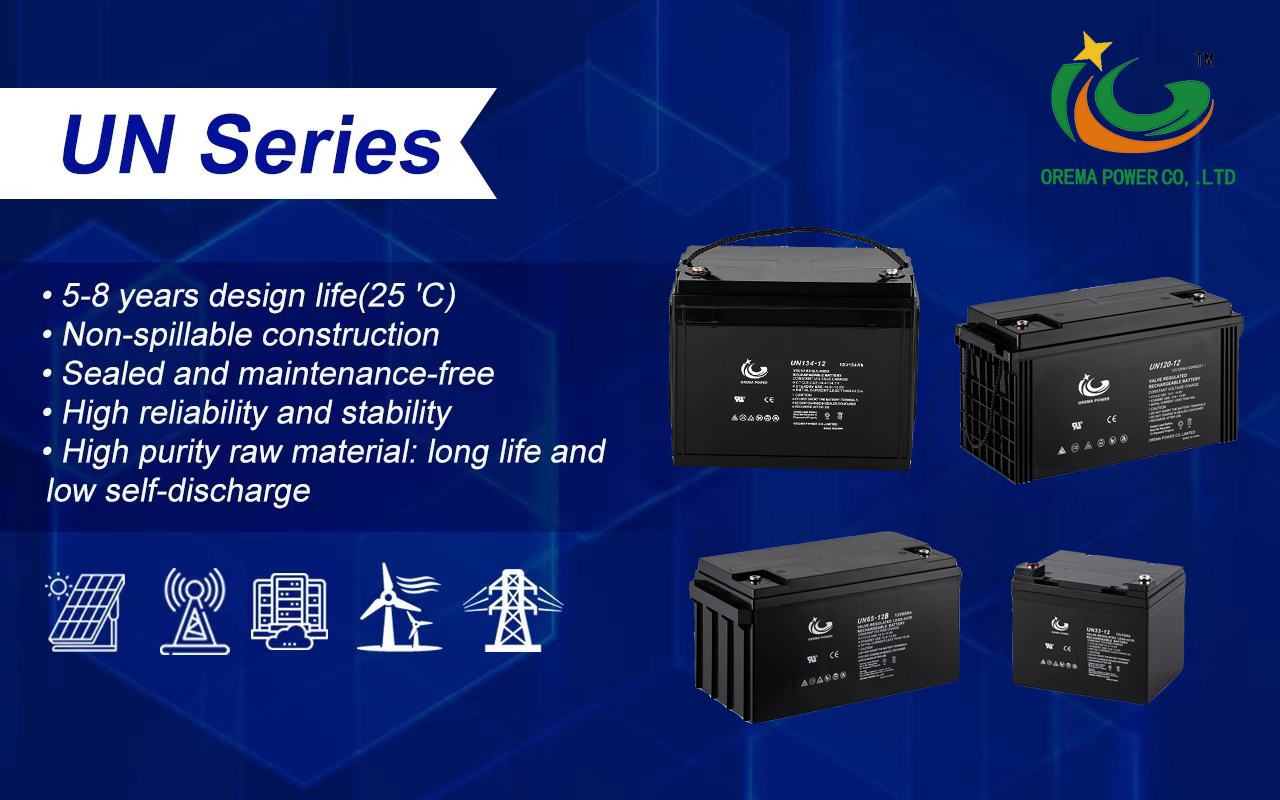
Innovative AGM Technology:
At the heart of OREMA UN Series 12V VRLA Batteries is the advanced Absorbent Glass Mat (AGM) technology. This technology ensures safety and flexibility in installation by absorbing the electrolyte in a fiberglass separator. It effectively eliminates the risk of leakage, provides excellent resistance to vibration and shock, and maintains a low self-discharge rate. This versatility makes them ideal for both long-term storage and demanding usage scenarios.Key Features of OREMA UN Series 12V lead acid battery:
- Extended Lifespan: Designed to last 5-12 years at 25℃, these batteries offer exceptional longevity.- Spill-Proof Design: The non-spillable construction of AGM technology guarantees safety and ease of use.
- Zero Maintenance: These batteries are maintenance-free, adding to their convenience and reliability.
- High-Quality Raw Materials: The utilization of high-purity lead ensures a longer lifespan and minimal self-discharge.
Compliance and Quality Assurance:
OREMA 12V AGM batteries adhere to global standards, including IEC, BS, JIS, and EU regulations. UL and CE certifications, along with ISO45001, ISO 9001, and ISO 14001 certifications of our production facilities, reflect our commitment to quality and environmental stewardship.Applications of OREMA UN Series 12V Rechargeable batteries:
- Power for UPS Systems: Ideal for providing stable and uninterrupted power in UPS setups.- Emergency and Backup Power: Dependable in emergencies and power outages.
- Control Systems Support: Crucial for the continuous operation of control systems.
- Communication and Security Systems: Essential for maintaining communication and security infrastructures.
- Electric Power Systems: Suitable for EPS applications, offering consistent and robust power.
OREMA UN series 12V AGM batteries are not just about providing power; they are about delivering reliable, safe, and efficient energy solutions across a variety of applications. With OREMA, you choose more than a battery; you choose a partner committed to powering your success in the digital age and beyond.
12v AGM Batteries,12v AGM Battery,12V lead acid battery,12V Rechargeable batteries,12V VRLA Batteries
OREMA POWER CO., LTD. , https://www.oremapower.com