First, system overview
Radar is an electronic device that uses electromagnetic waves to detect a target and measure its position, speed, and other characteristics. It has the characteristics of finding the distance to the target, determining the target coordinate speed, and working around the clock. In order for the radar antenna to control the target in all directions of space, it is necessary to allow the light beam to move freely in a wide range and achieve scanning and tracking of the target. The mechanical axis of the antenna car moves with the command of the radar motion control system. The electric axis of the antenna is always aligned with the target, and the target object is accurately, quickly, stably and reliably captured and fed back to the monitoring station.
Second, the system requirements
1) The entire system requires all-weather work and is affected by adverse environments such as vibration, dust, and moisture.
2) The system is streamlined, the failure rate is low and the investigation is easy, the instruction cycle is short, and the real-time performance is strong.
3) The HMI has strong data processing capabilities and rich communication interfaces, such as a CAN bus with good real-time performance and strong error correction capability.
4) Data protection and encryption, system crashes can be restored with one click.
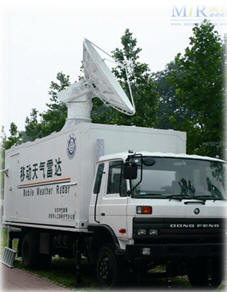
Radar antenna motion mode is divided into two kinds of pitch movement and azimuth movement. Pitch is caused by two master-slave servo motor geared to drive two screw rods. Then the connection antenna orientation is a servo motor gear directly connected to the antenna. In use, pitching works first, lifting the antenna to about 80 degrees to stop, and then working in the direction to continuously scan the air targets. The entire system is connected via CANBUS. The CAN bus has the characteristics of good real-time performance and strong error correction capability. The servo controller has a standard CANBUS interface and is connected to the PLC controller through the CAN bus. Then the HMI carries out DI, DO, AI and AO control of the PLC through its own CAN bus. In addition, the HMI can also accept the motor position signal to the PLC. The code parameters are modified to display the motor current, temperature, speed, limit status, etc. at the same time.
Fourth, the system block diagram
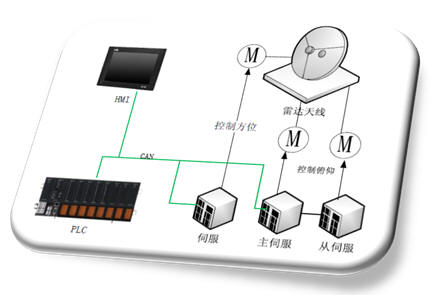
V. Product List
Part No | model | product description |
0010-040351 | PPC-1261T-0201/Touch screen | 12-inch low-power fanless tablet PC (resolution 800*600)/Intel ATOM N455 platform/CPU 1.66G clock frequency/2G DDR3 memory/500G hard disk/serial port×4/USB port×5/Gigabit Ethernet port×2 / CAN × 2 / VGA port × 1 / PS/2 × 1 / 1 audio interface / 9 ~ 30V DC power supply / aluminum alloy front / touch screen |
0020-057741 | PPC-1011-01/EC3-1817CLDNA/10.4" screen | 10.4 inch ARM industrial panel (with resolution 800*600/ i.MX53 Cortex-A8 800MHz/1GB DDR3 memory/5× serial port/ 2 10/100Mbps/ 2×CAN/ 5×USB2.0/ 1×HDMI/ 1× VGA/1 audio/1x mini-pcie/ 1xTF card/ 1xcfast/ aluminum alloy panel/ touch) |
Sixth, summary
EVOC CAN-bus Industrial Tablet PC has a rich product line covering ARM and X86 hardware architectures, supporting embedded operating systems (linux, andriod, wince) and desktop operating systems (winxp, win7), and fully supporting CAN standard messages Format and extended message formats, customers can directly use the machine's own CAN interface, no need for an external CAN card, greatly reducing the cost of customer equipment, while improving the reliability of the system. We believe that with the rich achievements and valuable technology deposits of EVOC Industrial Tablet PC in the automotive field, we will be able to create greater value for our customers.
Shenzhen ChengRong Technology Co.,Ltd. , https://www.chengrongstand.com