Foreword
The mechanical drive of the tapping drilling machine adopts linear guide and ball screw, clamping hydraulic pressure, and four axes working at the same time. After the workpiece is installed, it is processed one time at a time, which is 2 to 4 times of manual drilling, and can be operated by more than one person. Equipment, and reduce the labor intensity of workers. Rotary tables and fixtures are used to complete the movement and clamping of workpieces for automatic processing. Drilling slides and hole power heads are used to adjust the drilling volume and drill holes. Tapping slides and tapping power heads are used to adjust tapping throughput and tapping. The movement of the table, clamping and relaxation of the clamps, movement of the drilling slide and the tapping slide are controlled by the hydraulic system. The movement of the table and clamping and relaxation of the fixture are controlled by solenoid valves.
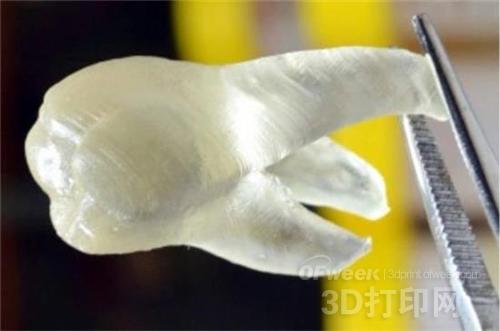
Drilling tapping machine system configuration No. Model and number Function
1 touch screen TG765-MT,
A touch screen screen has a main screen, parameter settings, product specification selection, manual, automatic screen, alarm screen, status monitoring. 2
PLC, XC3-32RT-E
Two two PLCs realize four-axis pulse control function and six station rotations. Input and output terminals are connected in series to realize the feeding and blanking process. 3 input and output expansion module
2 As the device uses many cylinders and photoelectric switches, two input and output expansion modules are required. 4 Servo DS3
Four four-axis servos perform chamfering, punching 1, punching 2, and tapping.
Workflow introduction
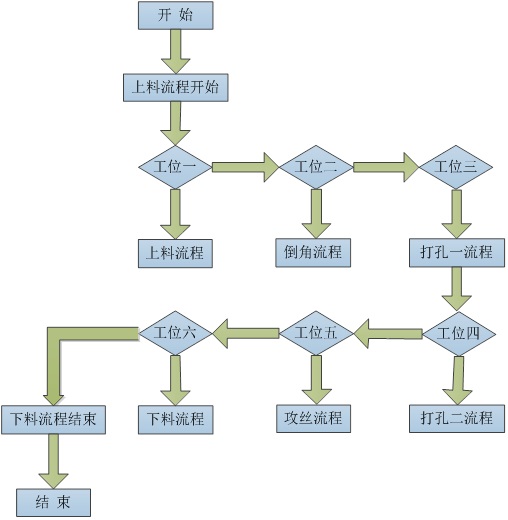
Process Introduction
During the feeding process, 8 cylinders are controlled to move. The final purpose is to send the cross material to the turntable.
Six position sensors are installed below the turntable action dial to let the device know which station he is in. Each time you perform an action, the turntable will rotate once.
Chamfer, punch, tap As long as the material reaches its specified position, he performs the action it wants to perform.
After the material is rotated and the other side is also executed, the material rotation is performed. Then continue chamfering, tapping, and punching.
After the blanking process material is processed, it is necessary to carry out the blanking.
In the implementation of the core six stations, feeding, spinning under the material, cutting, chamfering, tapping, drilling, must be used in conjunction, do not waste a little time, and ultimately high efficiency to complete the task.
PLC advantage
1, flexibility design: The entire system, has four product type specifications, in the course of use can be flexibly selected in the touch screen, to bring customers a lot of convenience.
2. Good operability: Click on the button directly on the touch screen to perform the required work, improve work efficiency, automate the drilling and tapping system, and set parameters flexibly for customers to design their own product specifications.
3, reliability is good: The system adopts XJ series advanced XC series PLC to realize the quantitative control algorithm. At the same time, by setting a plurality of timers and weight parameters, it can adjust the cutting process to the maximum extent to meet the needs of various occasions. And each timer and parameter can be adjusted; the stability of the product can make the equipment run stably for a long time.
4, compact structure, small size, light weight, easy to implement mechatronics.
5, PLC control system design, installation, debugging is convenient, because the software programming replaces the hardware wiring to achieve the control function, so that the installation workload is greatly reduced, the designer only needs a PLC to control the design of the system, and can be in the experiment Room for analog debugging.
6. With perfect functions and strong expansion capability, PLC can easily realize large-scale switch logic control. This is not achievable by general relays. There are many control functions within PLC, which realize process control, digital control, and networking functions.
The mechanical drive of the tapping drilling machine adopts linear guide and ball screw, clamping hydraulic pressure, and four axes working at the same time. After the workpiece is installed, it is processed one time at a time, which is 2 to 4 times of manual drilling, and can be operated by more than one person. Equipment, and reduce the labor intensity of workers. Rotary tables and fixtures are used to complete the movement and clamping of workpieces for automatic processing. Drilling slides and hole power heads are used to adjust the drilling volume and drill holes. Tapping slides and tapping power heads are used to adjust tapping throughput and tapping. The movement of the table, clamping and relaxation of the clamps, movement of the drilling slide and the tapping slide are controlled by the hydraulic system. The movement of the table and clamping and relaxation of the fixture are controlled by solenoid valves.
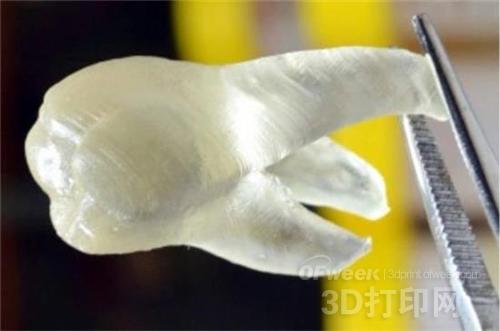
Drilling tapping machine system configuration No. Model and number Function
1 touch screen TG765-MT,
A touch screen screen has a main screen, parameter settings, product specification selection, manual, automatic screen, alarm screen, status monitoring. 2
PLC, XC3-32RT-E
Two two PLCs realize four-axis pulse control function and six station rotations. Input and output terminals are connected in series to realize the feeding and blanking process. 3 input and output expansion module
2 As the device uses many cylinders and photoelectric switches, two input and output expansion modules are required. 4 Servo DS3
Four four-axis servos perform chamfering, punching 1, punching 2, and tapping.
Workflow introduction
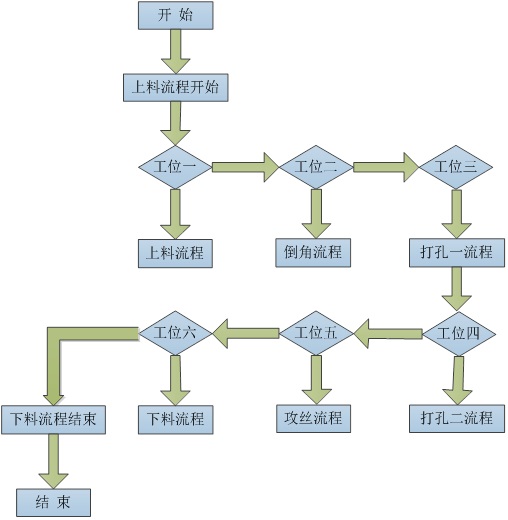
Process Introduction
During the feeding process, 8 cylinders are controlled to move. The final purpose is to send the cross material to the turntable.
Six position sensors are installed below the turntable action dial to let the device know which station he is in. Each time you perform an action, the turntable will rotate once.
Chamfer, punch, tap As long as the material reaches its specified position, he performs the action it wants to perform.
After the material is rotated and the other side is also executed, the material rotation is performed. Then continue chamfering, tapping, and punching.
After the blanking process material is processed, it is necessary to carry out the blanking.
In the implementation of the core six stations, feeding, spinning under the material, cutting, chamfering, tapping, drilling, must be used in conjunction, do not waste a little time, and ultimately high efficiency to complete the task.
PLC advantage
1, flexibility design: The entire system, has four product type specifications, in the course of use can be flexibly selected in the touch screen, to bring customers a lot of convenience.
2. Good operability: Click on the button directly on the touch screen to perform the required work, improve work efficiency, automate the drilling and tapping system, and set parameters flexibly for customers to design their own product specifications.
3, reliability is good: The system adopts XJ series advanced XC series PLC to realize the quantitative control algorithm. At the same time, by setting a plurality of timers and weight parameters, it can adjust the cutting process to the maximum extent to meet the needs of various occasions. And each timer and parameter can be adjusted; the stability of the product can make the equipment run stably for a long time.
4, compact structure, small size, light weight, easy to implement mechatronics.
5, PLC control system design, installation, debugging is convenient, because the software programming replaces the hardware wiring to achieve the control function, so that the installation workload is greatly reduced, the designer only needs a PLC to control the design of the system, and can be in the experiment Room for analog debugging.
6. With perfect functions and strong expansion capability, PLC can easily realize large-scale switch logic control. This is not achievable by general relays. There are many control functions within PLC, which realize process control, digital control, and networking functions.
Lifting Columns,Lifting Column,Linear Servo Actuators,Linear Servo
Kunshan Zeitech Mechanical & Electrical Technology Co., Ltd , https://www.zheteswitches.com