The CNC system is the core of all CNC equipment. The main control object of the CNC system is the displacement of the coordinate axis (including moving speed, direction, position, etc.), and its control information mainly comes from CNC machining or motion control programs. Therefore, as the most basic components of the numerical control system should include: the program's input / output device, numerical control device, servo drive these three parts.
(1) Input/output device The input/output device functions to input and output data such as CNC machining or motion control programs, machining and control data, machine parameters, coordinate axis positions, and status of detection switches. The keyboard and display are the most basic input/output devices necessary for any CNC device. In addition, depending on the CNC system, it can also be equipped with optoelectronic readers, tape drives or floppy disk drives. As a peripheral device, a computer is one of the commonly used input/output devices.
(2) Numerical control device The numerical control device is the core of the numerical control system. It consists of input/output interface lines, controllers, operators, and memory. The function of the numerical control device is to compile, calculate and process the data input by the input device through internal logic circuit or control software, and output various information and instructions to control various parts of the machine tool to perform prescribed actions.
Among these control information and commands, the most basic are the feedrate, feed direction and feed displacement command of the coordinate axes. It is generated after the interpolation operation, and is supplied to the servo drive, which is amplified by the driver and finally controls the displacement of the coordinate axis. It directly determines the movement path of the tool or axis.
In addition, depending on the system and equipment, such as: on the CNC machine, there may be spindle speed, steering and start and stop commands; tool selection and exchange instructions; cooling, lubrication device start and stop commands; workpiece loose Open and clamp commands; auxiliary instructions such as indexing of the workbench. In the numerical control system, they are provided to the external auxiliary control device through the interface in the form of signals. The auxiliary control device performs necessary compiling and logic operations on the above signals, and amplifies and drives the corresponding actuators to drive the mechanical parts of the machine tool and hydraulic pressure. Auxiliary devices such as pneumatics complete the actions specified in the instructions.
(3) Servo drive The servo drive is usually composed of a servo amplifier (also called a driver, a servo unit) and an actuator. On CNC machine tools, AC servo motors are currently used as actuators; linear motors have been used on advanced high-speed machine tools. In addition, DC servo motors are also used on CNC machine tools produced before the 1980s; for simple CNC machines, they are also useful as actuators. The form of the servo amplifier is determined by the actuator and must be used with the drive motor.
The above is the most basic part of the CNC system. With the development of numerical control technology and the improvement of machine tool performance level, the functional requirements of the system are also increasingly enhanced. In order to meet the control requirements of different machine tools, the integrity and uniformity of the CNC system are guaranteed, and it is convenient for users to use. The system generally has an internal programmable controller as an auxiliary control for the machine. In addition, on the metal cutting machine, the spindle drive can also be a part of the CNC system; on the closed-loop CNC machine, the measuring and detecting device is also essential for the CNC system. For advanced numerical control systems, sometimes even computers are used as the human-machine interface and data management and input/output devices of the system, so that the numerical control system has stronger functions and better performance. In short, the composition of the CNC system depends on the performance of the control system and the specific control requirements of the equipment. The configuration and composition are very different, except for the three basic components of the input/output device, numerical control device and servo drive of the machining program. In addition, there may be more control devices.
Flat Ethernet Cable with two RJ45 connectors on each end. CAT8 Ethernet Cable is the highest level in Network Cable territory. And all cat8 cable are backward compatible with CAT7 Ethernet Cable and CAT6 Ethernet Cable as well as CAT5E Ethernet Cable. Standard RJ45 Lan Cable protect against EMI/RFI interference, accurate data transfer and reliability
Range of application-perfect for network adapters, Hubs, Routers, DSL/Cable Modems, PS3, PS4, X-box, patch panels and other high performance networking applications.
Flat Patch Cable include CAT8 flat network cable, CAT7 flat network cable, CAT6 flat network cable, CAT5E flat network cable.
CAT8 flat patch cable as below:
Product Information:
1. Frequency - 2000 MHz
2. Transmission Speed - 40 GB
3. Available Length - 0.5m~20m
4. Connectors - Gold Plated RJ45 or Nickel Plated RJ45
5. Condcutor- 26AWG (America wire gague) or 28AWG or 30AWG
6. Cable Construction - Shielded
7. Jacket- PVC
8. Install - Used indoor, in-wall and in the ceiling
9. Different color and different model for your choice.
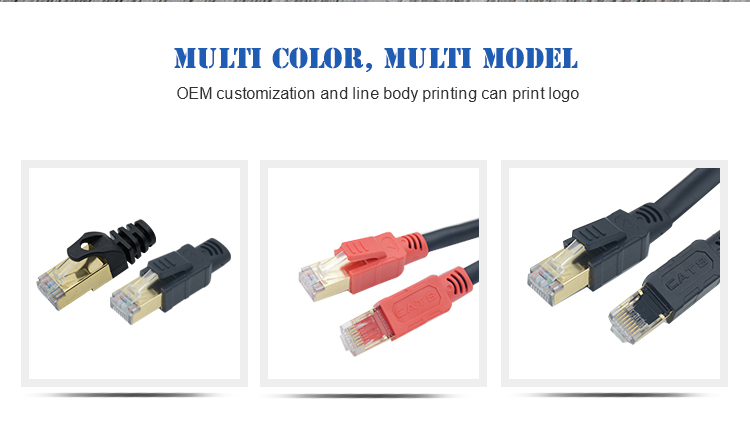
The unique flat cable shape allows for a cleaner and safer installation. You can easily and seamlessly make the cable run along walls, follow edges&corners or even make it completely invisible by sliding it under a carpet.
Applications: Computer, Router, TV, Interchanger, Concentrator, ADSL, Set-top box And So on.
Cat8 Flat Ethernet Cable,Flat Cat8 Cable,Flat Network Cable,Cat8 Ethernet Cable Flat
Shenzhen Kingwire Electronics Co., Ltd. , https://www.kingwires.com