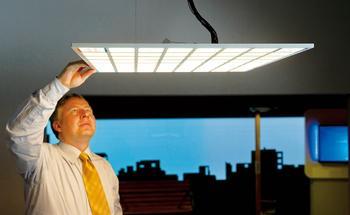
Organic light-emitting diodes (OLEDs) had a market size of only 500 million U.S. dollars in 2009, but they have continued to attract investment from the industry in subsequent years, which is really interesting. In fact, the reason why OLED has sparked an upsurge of development is partly due to its use on mobile phone screens such as the Samsung Galaxy series. The introduction of mobile screens has enabled OLED revenues to climb to $3 billion in 2011 and reached in 2012. 6 billion US dollars.
In addition to mobile phone screens, lighting is another potential application for OLEDs. Although OLED lighting currently accounts for only a small part of the overall output value, the huge potential lighting market is expected to bring new revenue opportunities to OLED players.
LED efficiency / cost advantage OLED lighting also needs time to develop
At this stage, LED lighting luminous efficiency is 110 lumens per watt (lm / W), while commercial OLED products up to 60lm / W; As for costs, LED technology costs almost $ 5 / 1000 lumens (klm), OLED is about 350 USD/klm indicates that there is still a clear gap between the two technologies in the development of lighting applications. As a result, OLED technology is bound to take advantage of the unique advantages of its light is not dazzling, the lamp size can be made large and flat, in order to successfully seize the lighting market a place.
Compared with standard LEDs and other light sources, the need for shades to cover strong light may cause problems of vision loss. The OLED light source may provide illumination without shading, and is another lighting future that is still in development; furthermore, OLEDs may be used. The use of many different styles of material combinations and structures has the potential to dramatically increase luminous efficacy.
Currently, OLED manufacturers have increased the efficiency by increasing the driving current, but at the cost of a shorter device lifetime; at the same time, the luminescence efficiency can also be improved by stacking OLED structures in series, such as stacking two different structures during the deposition process. Together, driving with the same current will produce almost twice as much light. As a result, related industries can also use lower currents to drive stacked OLED panels, which can generate the same luminosity and increase reliability, overcoming the problems of high OLED current lifetime.
Although OLED lighting has potential for development, if it is regarded as a direct rival of LED in the lighting market, the difference in performance and cost may make OLED out in the foreseeable future. However, under the circumstance of OLED lighting technology and luminaire design, there are still two kinds of solid-state lighting technologies that need to exist at the same time. This is not related to whether OLEDs are required to compete with LEDs or not. The application is not exactly the same.
Considering technical differences other than cost and luminous efficiency, if the OLED fully achieves the same level as the LED, it will be a great achievement. In general, commercial LED products have a guaranteed lifetime of 20 to 25 years, and OLEDs only have 5 to 10 years. The main reason is that some materials in OLED are eroded at a faster rate than other materials, and the color will change, which is in some industries or automobiles. The application is unacceptable.
Material cost/barrier layer designed to break through OLED
The OLED material is etched because the organic material layer is sensitive to oxygen and moisture and must be carefully covered and protected with a Permeation Barrier. This poses a serious challenge to the elastic design of the OLED panel. Currently, it is difficult for manufacturers to make Cost-effective, transparent and bendable, and resistant to high temperature infiltration barriers during the manufacturing process.
At this stage, 100% of commercial lighting OLEDs use glass as the substrate for the thin film layer and place a glass plate as a physical protective layer and a moisture/oxygen barrier layer (Fig. 1). However, even with these components, OLED organic materials are used. It will still be eroded in high temperature environments. This situation will cause problems with accelerating pressure testing above 85°C.
On the other hand, for manufacturers with traditional lighting backgrounds, it is difficult to use OLED professional technology as lighting equipment, so OLED industry operators must also propose countermeasures to overcome the commercial and technical challenges of lighting. In particular, OLED panels and traditional lighting equipment manufacturers are now going their own way. In a short period of time, OLEDs will hardly penetrate the lighting market. The possible solution in the future is for OLED panel manufacturers to produce their own lighting equipment, which will be promoted by technology rather than commercialization. Traditional marketing strategy.
But another challenge is how to reduce OLED manufacturing expenditures. Three major problems can be found in the cost breakdown of commercial OLED panels. First, the manufacturing yield of OLEDs is very low. Manufacturers do not have sufficient control capability, technology or experience in high-yield manufacturing processes. Second, the cost of constructing OLED production lines is high. For example, OSRAM has invested 20 million pounds in OLED pilot production line in Regensburg, Germany. The third is the high cost of materials and equipment, and the high cost of OLED production lines. Because this is an emerging technology, there is no standard equipment.
Since each OLED trial production line will take several months to build, equipment manufacturers also share the cost. Although OLED manufacturers claim to switch to ultra-thin layers, which can offset the high cost of complex molecular materials, most analysts believe that it is only half true because the cost of materials is related to the materials used in manufacturing and lighting panels. Most of the production uses The material is deposited on the reactor wall or is not deposited at all, causing material waste.
In any case, OLED lighting has certain application advantages, and there are still many opportunities for improvement in the future of manufacturing technologies. Therefore, YoleDeveloppement predicts that the cost of OLEDs in the next two years is expected to drop to the current level of one-third, mainly due to the introduction of newer generations into the industry. The production equipment will use a larger mother glass substrate in the deposition reactor to improve the mass production efficiency. At present, manufacturers are most commonly used 47 cm × 37 cm of the second generation of mother glass, can produce a few standard 10 cm × 10 cm OLED panel.
Supply chain to fully support large-size OLED commercial useable
In the future, the final product of mother glass and OLED panels will continue to evolve in the direction of large dimensions. The main consideration is that 10 cm × 10 cm OLED panels will not be sufficient to illuminate a room. Ten or more films may be required, which will result in additional costs for each panel. Such as cutting and connecting components required, if only a large panel, those manufacturing costs will naturally reduce.
However, for large-sized OLED panels, how to obtain the same luminosity across the entire panel surface will be a challenge. Many companies have already solved this problem, for example, OSRAM has introduced metal meshes into electrodes to improve the light emission balance. According to the latest research report from Yole Developpement, before a major breakthrough in the development of large-size OLED panels, OLED lighting can only achieve a small market, focusing on general lighting and automotive applications.
The initial integration of OLED technology will be special lighting, followed by high-end office and commercial applications; in the medium term, high-end residential lighting equipment will gradually use OLED, and the overall market penetration will reach 1.5% by 2020. At $1.7 billion (Figure 2), 80% of it is for general lighting applications.
For OLEDs, the development of new materials is the primary focus. Therefore, a country or region with strong chemistry may be the first point of observation for the birthplace of stronger companies. Second, the organic OLED market is actually a screen, and Asian countries have great investment in this area, especially in South Korea. At present, Samsung SDI and LDK are the two major manufacturers of OLED screens, while South Korea’s Chemical strength is also very strong. It is worth noting that Germany also has a very strong background in chemical research, and there are already emerging OLED industry players.
As the OLED future looks like this, manufacturers of glass, plastic or metal foils, including equipment manufacturers, suppliers of fluorescent and phosphorescent materials, polymer material developers, and flexible substrates have all invested heavily, even Several companies are actively developing new OLED structures, packages, plastic or special technical solutions that penetrate barriers and new electrodes. There are so many companies involved in the field of OLED lighting may be quite surprising, but how many companies involved in the entire value chain, not just how many manufacturers are manufacturing OLED panels.
Therefore, when technology historians review and evaluate the contribution of OLED lighting, they may find that their impact exceeds the market share of the performance, and many current practitioners of this technology emphasize that the new materials of OLED lighting that are in development will make The world is better. However, not all manufacturers are absolutely convinced that the OLED lighting market will be very large. They adopt a risk-dividement strategy, use investment funds to develop different applications, and use the research results simultaneously to develop organic or organic solar cells. In addition, good OLEDs Moisture infiltration barriers or soft ultra-thin glass can open up many new applications.
Easy Electronic Technology Co.,Ltd , https://www.yxpcelectronicgroups.com