The 2016 Autopilot Vehicle Development and Testing Technology Seminar, jointly hosted by Che Yun and Zosi Research and Development, was held in Shanghai from August 4th to August 5th. At the meeting, Zhou Yanwu, research director of Zosi Research Institute, introduced the relationship between the line-controlled brake system and driverless driving, as well as the status and trends of the line-controlled brake technology. Che Yun will organize the speech as follows.
This article refers to the address: http://
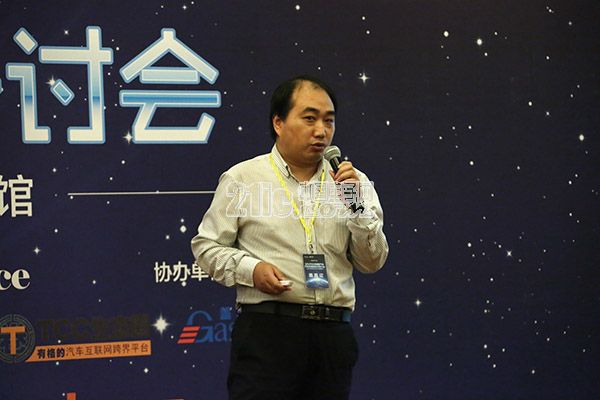
Zhou Yanwu, research director of Zosi Research Institute, knows that smart cars include sensing, control and execution. Among them, there are many sensors and controls. I will talk about this one today.
The wire control technology for throttle and steering is relatively mature. Let me talk about the brake system. No matter whether it is an unmanned vehicle or an autonomous vehicle, there is no mass production, so we need to find one from the cars that have been mass-produced now. Regarding the choice of models, some people will ask, why did you choose this car? Basically all the manufacturers, whether it is Google or Toyota, Honda, Nissan, GM, all the modifications are modified with pure electric cars or mixed electric cars.
Why are foreign big companies not using fuel trucks to refit? This is because the biggest advantage of a hybrid or pure electric vehicle is that it has a better line-controlled braking system.
The brake system requires a long time of technical accumulation and accumulation of brake data. In Chinese companies, there are very few brake system management. The best in China is the universal. At present, the unmanned vehicles in the colleges and universities are basically modified with fuel vehicles. Their steering system is externally mounted, with a Motor with a steering wheel. The brake system is controlled by PLC, and the brake is controlled by a motor. In fact, in this scheme, the total time required for the driver's reaction time plus the motor braking time is long, and thus the risk of being driven is higher. In other words, it can only be used for research and testing, algorithms for detecting sensors, etc.
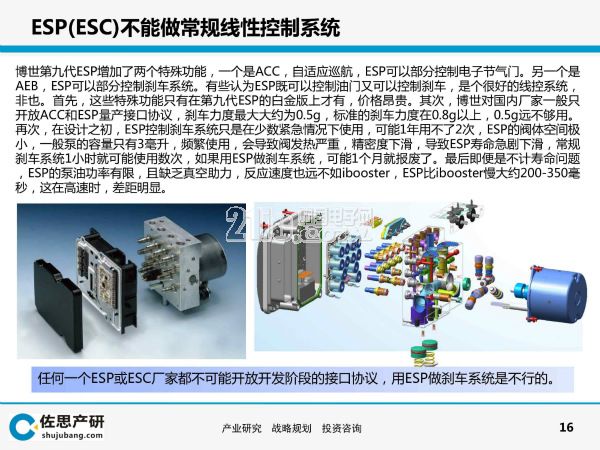
Next, I talk about ESP (some called ESC). Some people think that ESP can control both the throttle and the brakes. It is a good line control system, but it is not.
First of all, these special features are only available on the Platinum Edition of the ninth generation ESP and are expensive.
Secondly, Bosch generally only opens ACC and ESP mass production interface agreements for domestic manufacturers. The maximum braking force is about 0.5g, and the standard braking force is above 0.8g. 0.5g is not enough.
Third, at the beginning of the design, the ESP control brake system was only used in a few emergency situations and may not be used twice a year. ESP's valve body space is very small, the general pump capacity is only 3 ml, frequent use, will lead to serious valve heating, precision decline, resulting in a sharp decline in ESP life, the conventional brake system may be used several times an hour, if using ESP to do The brake system may be scrapped in a month. Finally, even if it does not count the life problem, ESP pump power is limited, and lack of vacuum boost, the reaction speed is far less than ibooster, ESP is about 200-350 milliseconds slower than ibooster, which is obvious at high speed.
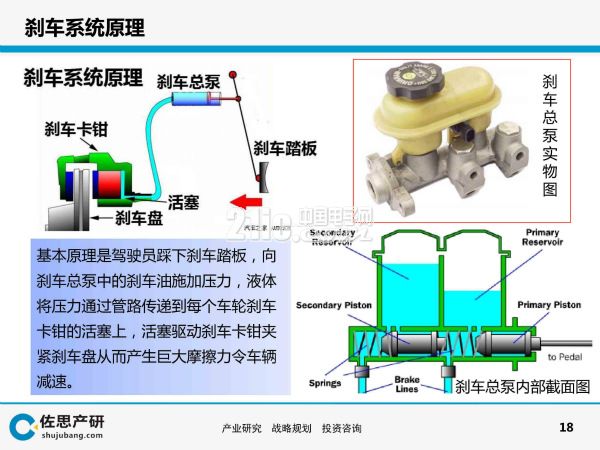
Why is the electric car line control better? The first generation of the line control system is EHB. Let me talk about the second generation of the line control system, which is the future EMB. EMB and EWB are true line-controlled brakes, and EHB barely counts line-controlled brakes, which still require a hydraulic system on a conventional car. The EMB and EWB are complete electromechanical systems without any hydraulic components. EWB was developed by Siemens and the biggest difference from the EMB system is its wedge coupling.
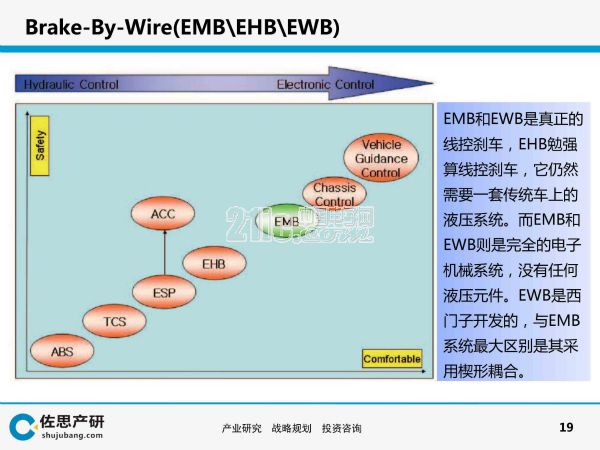
In 2001, there were hybrid cars, one was Toyota's Prius and the other was Mercedes-Benz. A set of brake systems EBC developed by Toyota and Bosch is mainly used in hybrid and electric vehicles. Mercedes-Benz began using the SBC brake system in 2001. In 2004 and 2005, about 3 million vehicles were recalled. It will no longer use this set and switch to the ABR system that the mainland has modified.
Toyota's EBC system is still in use today, which is currently recognized as the best brake energy recovery system. The system was also the most complicated, and the Germans began to make a system similar to it, but the Germans found that there were too many pipes and the hydraulic system was too complicated and it was easy to go wrong. However, Toyota's Japanese manufacturing process surpassed that of Germany, and it has no problem to do. It has been used since 2001. Toyota's second-generation electric car brake system in 2005, because the system is very expensive, can only be used in top cars.
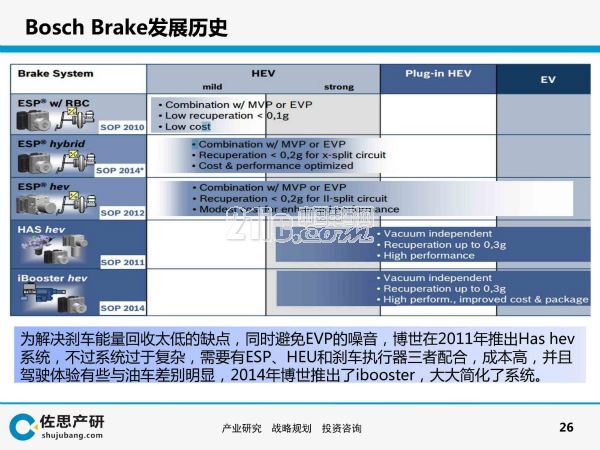
The picture above shows the history of Bosch's brake system development. EVP (Electronic Vacuum Power Pump) is now the perfect solution, completely replacing the vacuum booster. At present, it is the most suitable for wire-controlled brake. Because Bosch took a step forward, its two rivals, Continental and Trina, stepped up to combine vacuum boost and ESC. There is no actual mass production of this kind of scheme, and it is expected that there will be people around 2018.
We say that the ultimate goal of the brake system is the EMB electronic brake system. The biggest advantage of EMB is that the reaction time is short, and the hydraulic pressure is directly controlled by the electronic. If the wheel cylinder is controlled by the hydraulic pressure, the reflection time is increased. For unmanned vehicles, it is necessary to minimize the reaction time of its entire actuator. Therefore, EMB is the most suitable, can achieve 90 milliseconds at the earliest, and theoretically can do better.
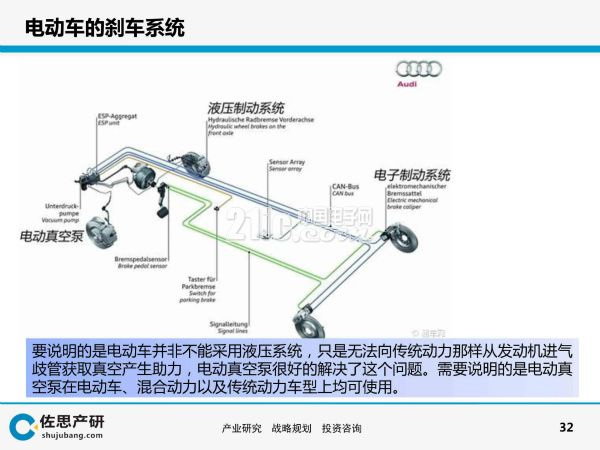
This is the Audi R8 e-tron brake system, now it is the first system to use EMB, and it only uses the EMB system in the rear wheel, the front wheel is still the traditional hydraulic system. Because the EMB system is not mature enough, it cannot be used alone.
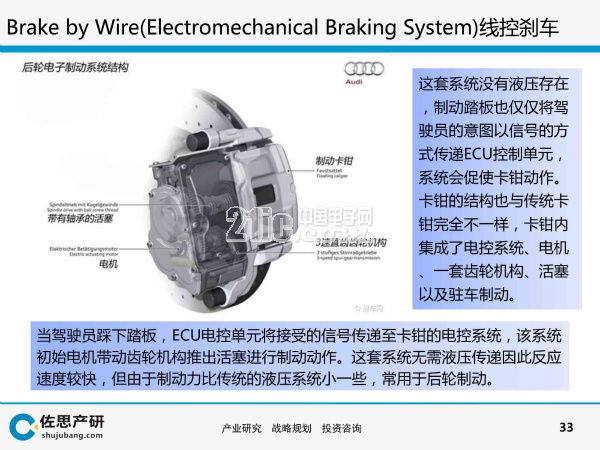
The most prominent advantage of EMB is security. First of all, the reaction time of a traditional brake system is preferably 300-400ms, and the EMB is only 90ms, the braking distance can be shortened by 60%, and the safety factor is relatively high. Secondly, it has no hydraulic system and no liquid leakage. Will be more reliable. Especially for electric vehicles, there is a risk of a short circuit if there is a liquid leak.
The biggest advantage of EMB can be bypassed by Bosch, Continental, Tianhe and other manufacturers. It has no backup system. It is purely wire-controlled, and it is difficult to set up a redundant system. The shortcoming of EMB is that the braking force is insufficient. It is made of permanent magnet motor. The volume cannot be too large and can only be done inside the rear wheel.
For Chinese manufacturers, the brake system basically can't get rid of Bosch. No matter the sensors and control systems are doing well, the actuators must communicate with them. Bosch does not let go of the interface or only let go of very few interfaces. The development of people and vehicles is completely limited. If Chinese companies do EMB in four rounds, they can circumvent Bosch, but the EMB system has many shortcomings. I think that at low speeds (about 50-80km/h), the shortcomings of EMB are not very obvious, so it can be used. At present, the best EMB in China is probably a universal one.
Distribution Transformer,Electric Oil Type Distribution Transformer,Oil Type Distribution Transformer,Oil-Immersed Special Transformer
Shaoxing AnFu Energy Equipment Co.Ltd , https://www.sxanfu.com